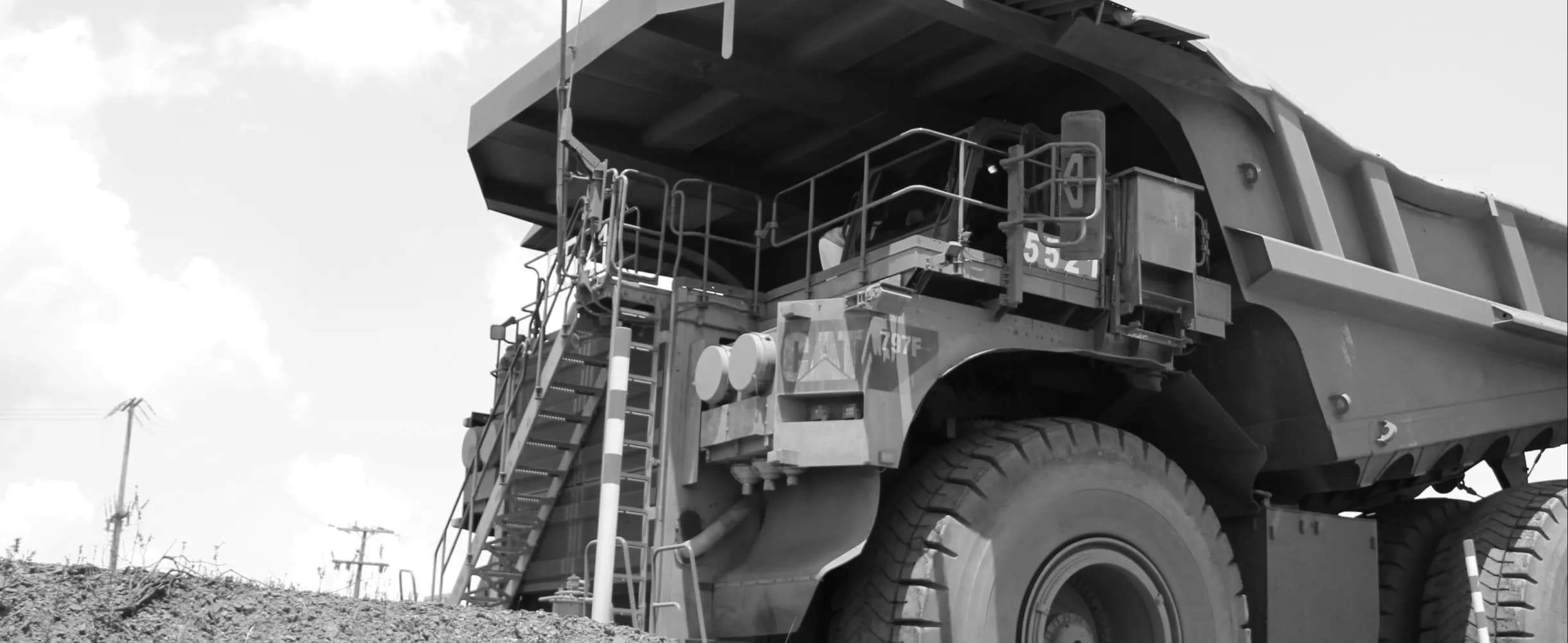
$5 million
Savings
300 hours
of downtime avoided
45h
of inspectors exposed to risk avoided
OVERVIEW
General context
Located in the state of Pará, Mosaico de Carajás is responsible for nearly 60% of all Vale's iron ore, with approximately 150 million tons of iron per year. It is also the largest open-pit iron ore mine in the world.
In this scenario, one of the main challenges was monitoring the condition of off-road vehicles such as drilling rigs, trucks, etc. To collect vibration data, for example, it was necessary to dismantle part of the external structure, making the process time-consuming and putting the safety of the technicians at risk. To increase safety and make data collection more practical, the Serra Norte Predictive Maintenance Supervision team at the Carajás Mine relied on the Dynamox Solution and DynaTrigger, which enables data collection synchronized with the asset's operation.
Success story awarded at the 25th Mining-Metallurgical Industry Excellence Awards at the 14th Opex 2023 Workshop.
Segment:
Mining
Sensors installed:
500 in vehicles
Assets monitored:
+40 vehicles
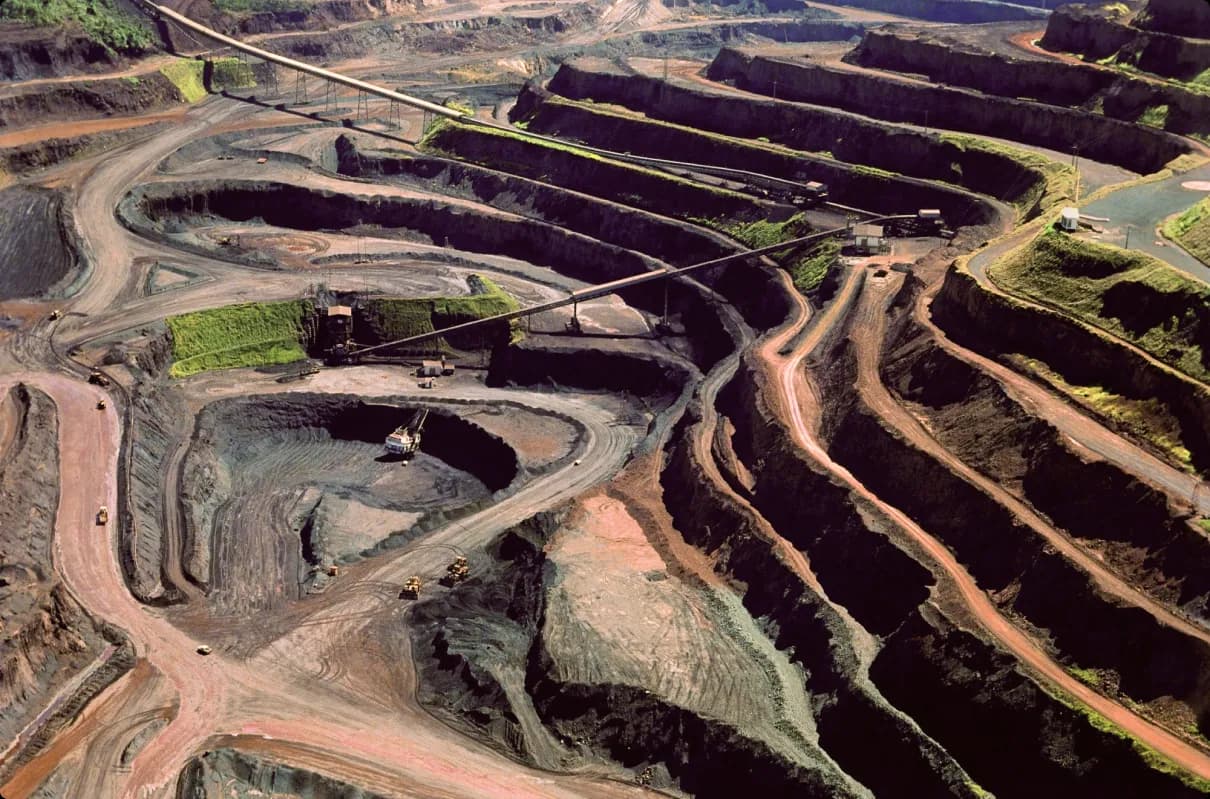
Vale | Carajás Mine.
RESULTS
Positive impacts for off-road vehicle monitoring, with significant figures
$2.6 million
Savings on miner machine maintenance*
$2.4 million
Savings on drilling rig downtime
45h
of inspectors exposed to risk avoided
300h
Downtime avoided
*The Dynamox Solution made it possible to monitor the force applied by the operator to the miners. This procedure has helped to prevent the bits from wearing out prematurely, avoiding the extra cost of replacing them earlier than expected.
TIMELINE
The process of signing up to Dynamox Solution
The implementation of this modernization in data collection took place in steps. Check out how it went at the Carajás Mine.
2021
2021
Manual collection via offline collector
The vibration collection procedure was carried out manually and offline, involving several professionals from different areas.
How it was done:
To monitor the wheel pinion on trucks, for example, the vehicle had to stop so that a professional could enter the truck's structure, remove the wheel pinion and position the accelerometer. The structure was then reassembled and only then was the data measured. Five professionals were involved in this activity. The process was similar for motors, pumps and compressors, impacting the production process and potentially causing safety risks. The inspection kept the equipment idle for around 2 hours or more, and was carried out periodically.
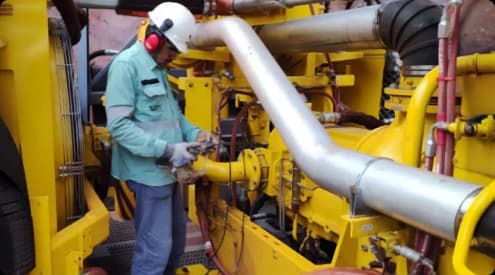
Inspector carrying out manual collection
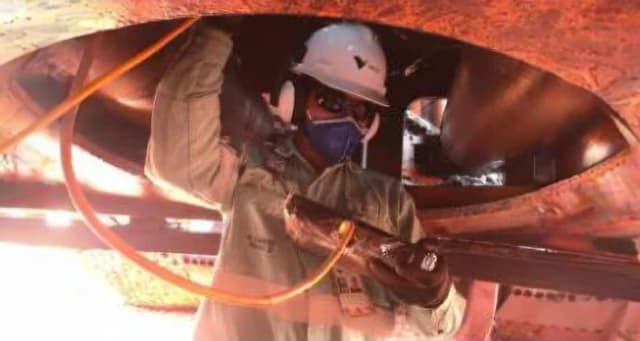
Inspector carrying out manual collection
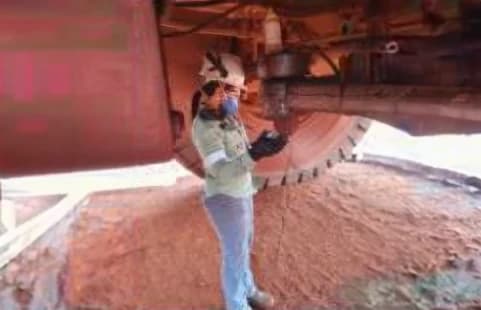
Inspector carrying out manual collection
2022
2022
Installation of wireless sensors and collection via App
To reduce this downtime, increase data reliability and team safety, the solution was to use Dynamox wireless vibration and temperature sensors.
In off-road vehicles, the sensor is fixed inside the wheel to monitor vibration and temperature. Data collection was based on the truck moving at a continuous speed along a short predetermined path. At this point, the inspector remained at a safe distance and captured the information from the sensor with the tablet.
Inspector collecting remotely via app
10/2022
10/2022
Expansion of the number of assets with sensors
Based on the experience with the trucks, the team expanded the installation.
Assets monitored:
Drilling rigs
Loaders
Excavators
Components monitored:
Motors
Compressors
Pumps
Generators
Alternators
Among others
This is where drill rigs stand out. Complex equipment that operates intermittently.
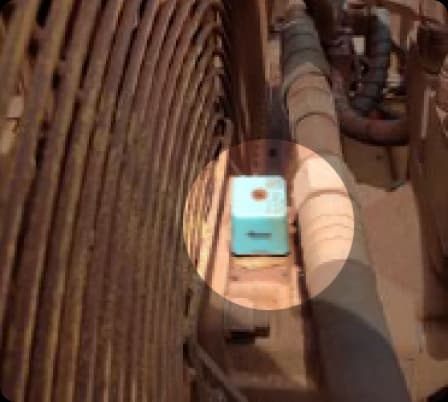
Fan motor
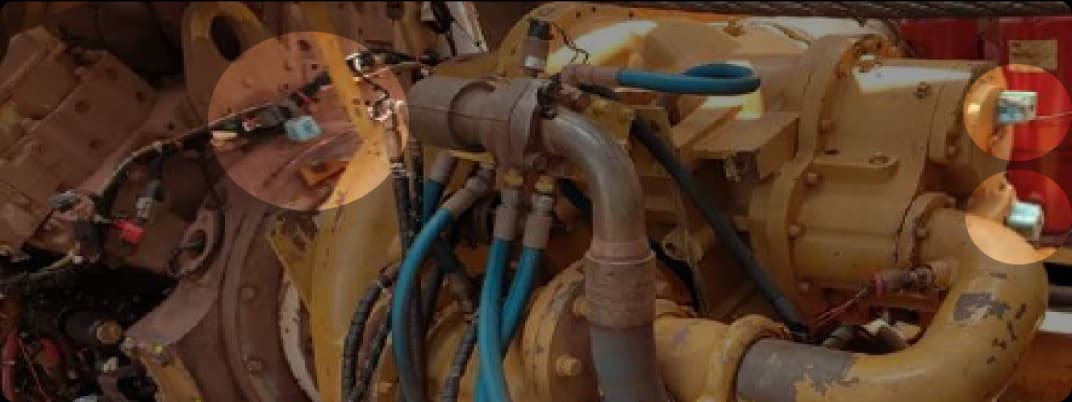
Diesel engine/compressor
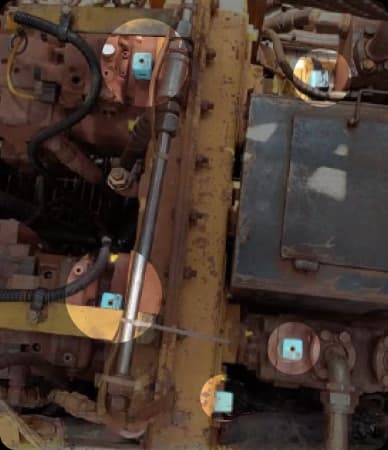
PTO/hydraulic pumps
12/2022
12/2022
Collection automation
With an increase in the number of sensors to intensify monitoring, we sought to optimize the process through the Gateway, a collection automation device installed in the vehicles. These devices collect data via Bluetooth and send it to the Dynamox platform via mobile networks. However, another challenge was still present: data repeatability. Faced with this, Vale and Dynamox began to explore options to solve this problem.
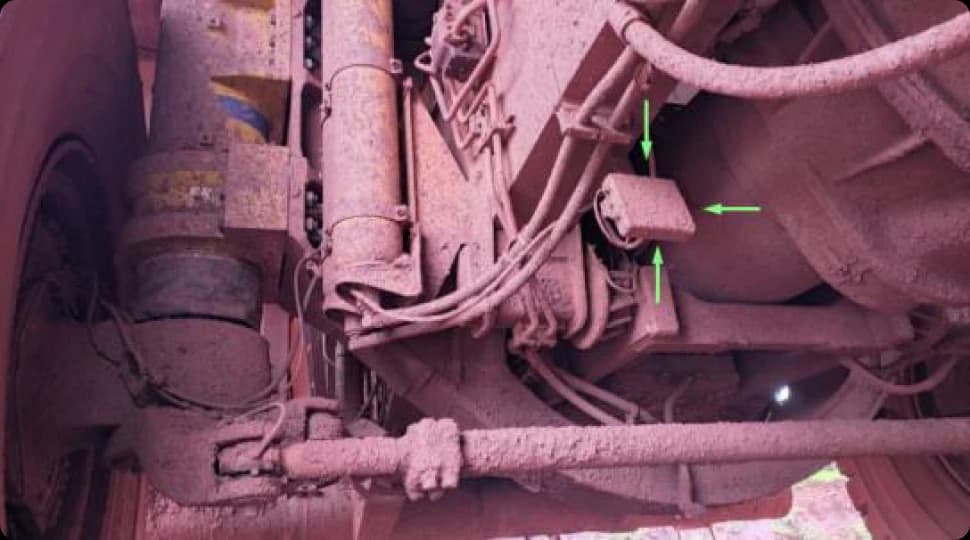
Gateway installed in off-road truck
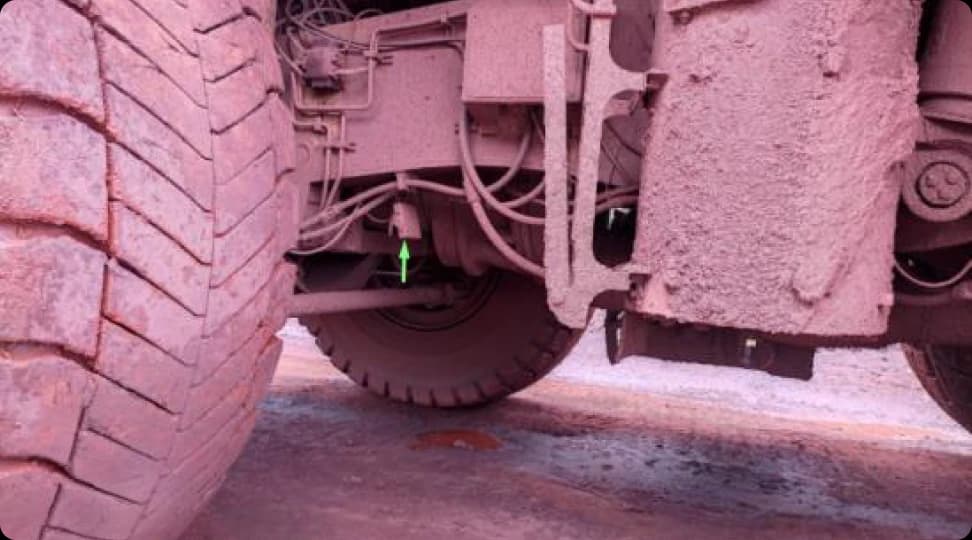
Gateway installed in off-road truck
2023
2023
DynaTrigger: functionality to optimize data collection
DynaTrigger is a Dynamox solution that works like a "Gateway trigger", mainly applied to autonomous drilling rigs. This allows data collection to be triggered when an external signal, linked to the equipment's operating condition, is sent to the Gateway. In this way, collection is carried out at the most appropriate time, synchronized with the asset's operation.
How it works:
The DynaTrigger allows you to define various drive parameters, either simple or combined. From this, the Gateway is now able to understand the asset's operating behavior and DynaTrigger collections at specific moments in the equipment's operation, such as when a certain component is activated or when it enters a specific rotation.
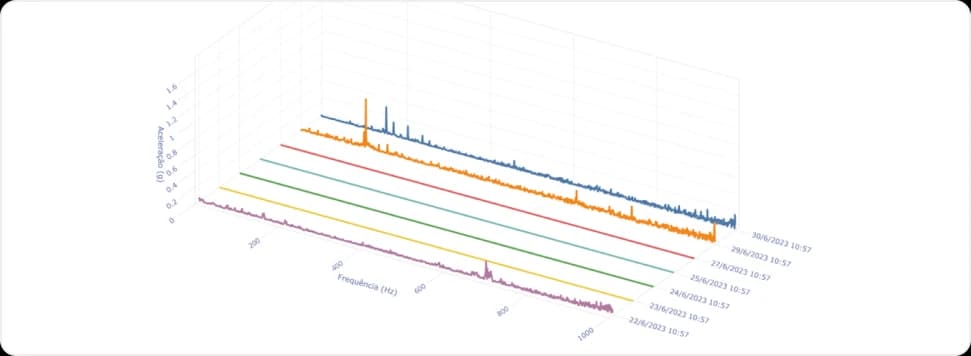
Waterfall waveforms before DynaTrigger
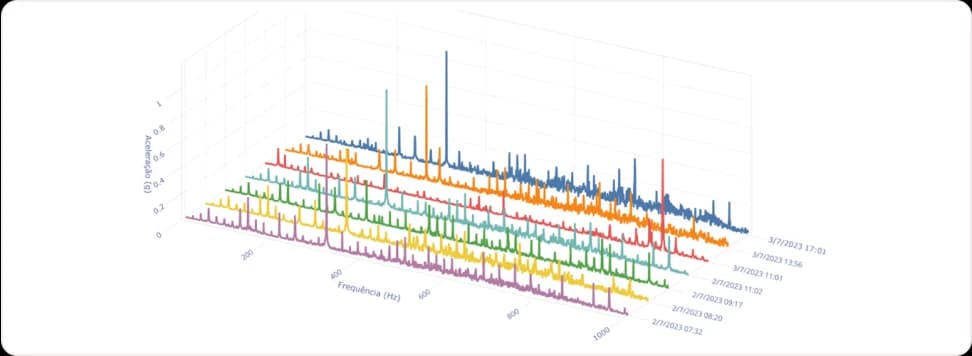
Waterfall waveforms with DynaTrigger
DynaTrigger is part of the efficient vibration monitoring strategies, which, together with the visual management module, allows for more assertive decision-making.
2023
2023
Visual Management
Visual Management allows you to visualize the plant's production flow and its health indicators. This way, you can see the impact of a machine stoppage on the process as a whole and have organized information on each asset.
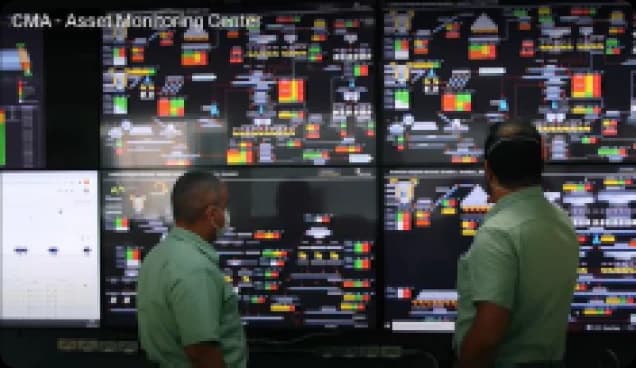
AMC - Vale
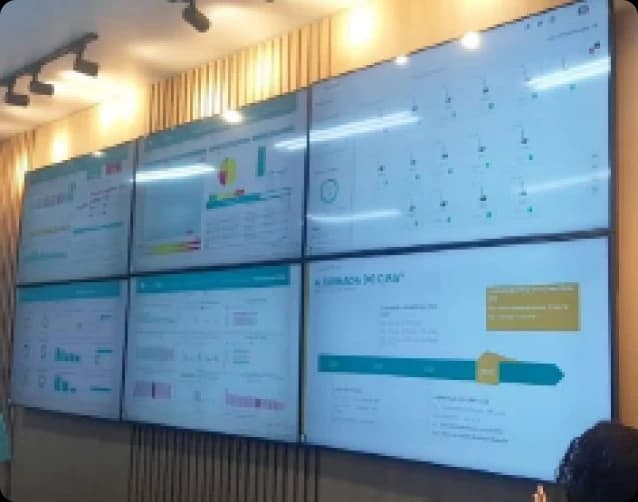
AMC - Vale
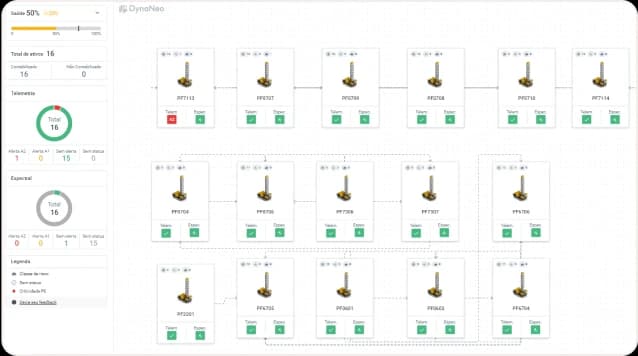
Visual Management dashboard - Dynaneo
2024
2024
Expansion and improved use of the Solution
To make maximum use of the solution, Vale's team is in the process of installing Gateways in all the trucks that are already sensorized in order to automate collection.
Pit Stops
Another improvement that is being implemented is the creation of pit stops: locations with Gateways strategically positioned to collect vehicle sensing data.
Other vehicles:
At the same time, a study is underway to implement the solution in other vehicles that are not yet sensorized, such as the Caterpillar 797 model.
DRILLING RIGS
Learn more about the project's gains
Discover all the features and applications of the Dynamox Solution for monitoring assets and managing maintenance actions.
Elimination of collections from idle machines
Enabling the monitoring of trends and the evolution of defects
Remote collection via private LTE network
Increased production by not stopping assets
Removal of employees from being exposed to risky operations
Collections with equipment at the same speeds
Applying the solution to 15 drilling rigs:
$2.3 million
Production deficit avoided by predictive downtime
$44,800
Powertrain savings
2700 min
Reduction in risk exposure with each collection
FULL MONITORING
Bring the Dynamox solution to your industry!
Discover all the features and applications of the Dynamox solution for monitoring assets and managing maintenance actions. Fill in the form below and speak to one of our experts.
In case you are a reseller, click here.